
In Focus: How Scanstrut’s in-house team beats drudgery
Earlier this month (October 2023), Scanstrut was delighted to announce that ATMOS, an in-built air station for inflating paddleboards, fenders and the like, had won the prestigious IBEX Innovation Award in the Mechanical Systems category.
The product marks a step up from Scanstrut’s regular mounts, chargers and seals. It’s been making installation solutions for marine electronics since 1986, but ATMOS represents an entirely new category for Scanstrut, a departure from its traditional product lines.
At the time of the award one of the judges, Ryan Gullang, praised ATMOS as an elegant and effective solution to the relative drudgery of inflating water toys.
Beating drudgery has been one of Scanstrut’s core principles – not that the Exeter-based company uses those words. The way the company puts its mission is to develop “anything that makes boating easier and more convenient,” according to George Bowles, head of design. He’s been in place for a decade and has worked on mounting solutions for marine electronics, to wireless charging systems for boats.
Now he looks after the in-house design team, which works across Scanstrut’s core markets – marine, RV, agri-off road and industrial. The company utilises product developments in each area to feed the design in another, and Bowles says the current focus is very much on “exploring ways to integrate cutting-edge technology into our products, such as advanced materials and wireless power transfer.”
The design team has always worked in-house – occasionally seeking support for electronics development. Bowles notes that having an in-house design team is obviously more flexible – but he says it’s also faster and the designers have a much better understanding of Scanstrut products in general and how they need to be built to suit existing and potential customers.
The team’s responsible for developing a mix of what Bowles terms ‘bold projects’ like ATMOS and Waterproof 12V Wireless Power Transfer, as well as more bread-and-butter projects like cable seals and mounts.
In fact, Bowles characterises ATMOS as ‘remarkably’ bold. This, he explains, is because of its multifaceted nature, with a new usage scenario, a fresh product type, and a step forward for the company’s business strategy. It was also a response to market need.
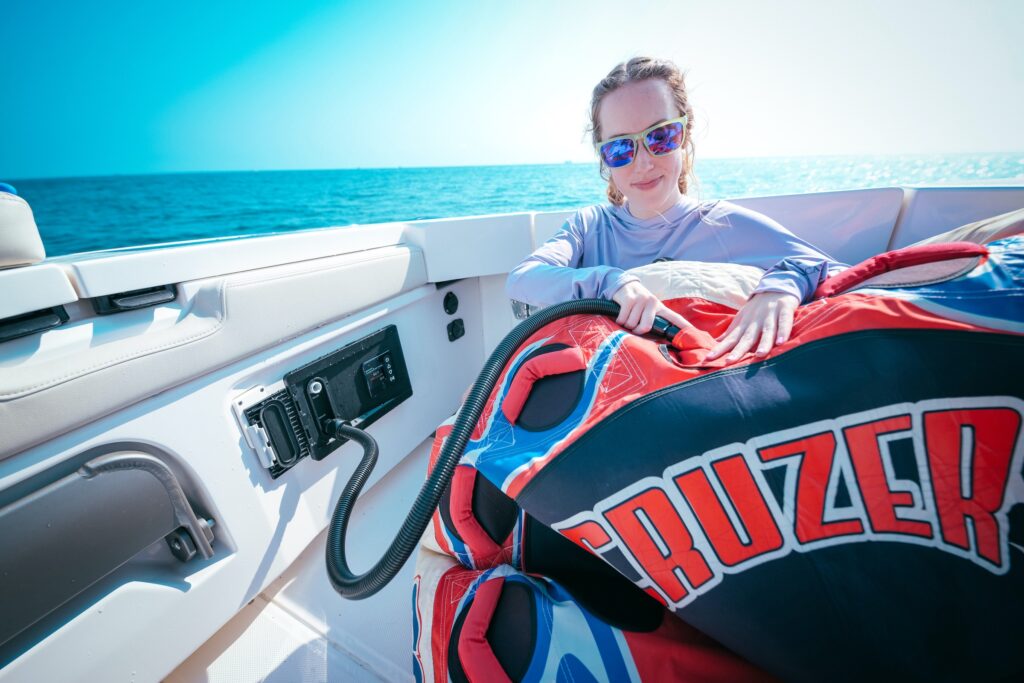
“The project evolved iteratively,” he says. “Through testing of existing pump products, the team identified ways to enhance product lifespan specifically in the context of boat usage. Remarkably, ATMOS reached a stage where it shares no common components with existing pumps. The user interface underwent significant improvements, and the range of included accessories expanded.
“The focus was not merely on improving functionality but also on making these pumps seamlessly integratable into boats, compatible with boat battery systems, and robust enough to withstand extreme conditions. The rigorous testing and development phase played a pivotal role in refining the concept.”
As well as ATMOS, Bowles says one of the team’s breakthroughs is the Scanstrut ROKK Wireless – Nano 10W. This is a waterproof wireless charging mount, designed specifically for boats. “It’s not just a wireless charger; it’s a complete problem solver of a product that has simplified the way boat owners charge and mount their devices while on the water, eliminating the need for cumbersome cables.”
Scanstrut aspires to bring the same level of innovation to the RV space and while marine may have been the initial focus, the company’s intention is to extend its innovative approach to both sectors.
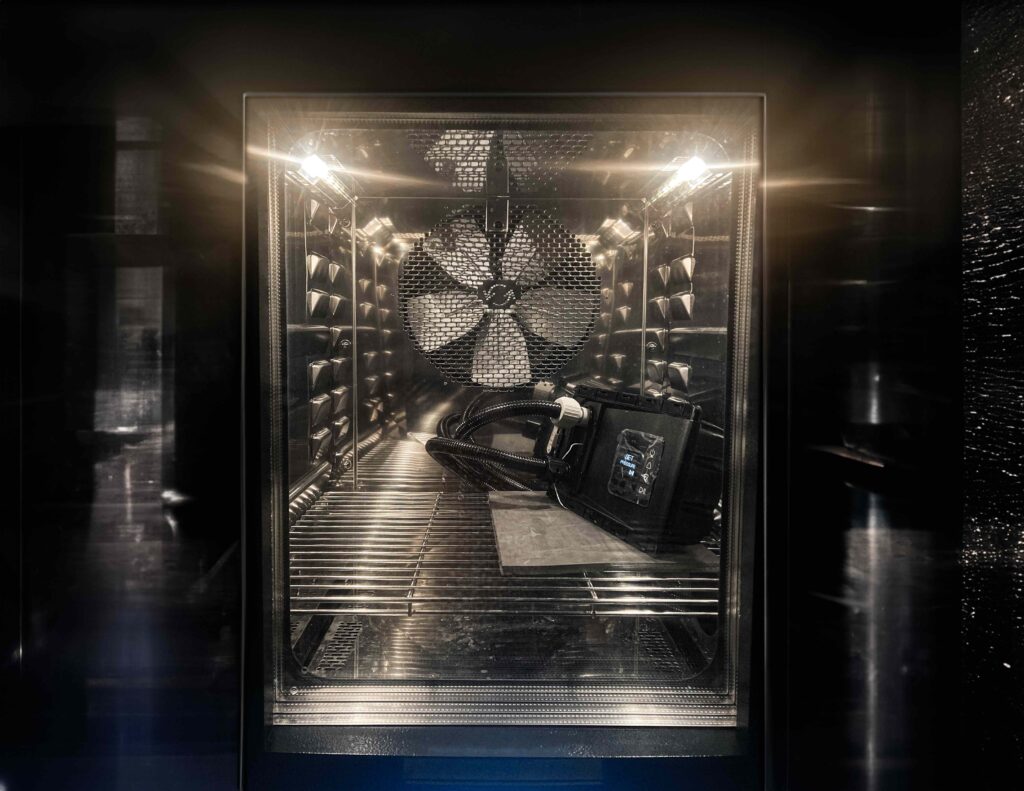
“Generally anything designed to withstand the marine environment will be a premium RV product,” says Bowles. “Understanding of key environmental factors and how to protect against them for minimal extra cost is key.”
The team collaborates closely with boatbuilders, electronics manufacturers, and end users to stay at the forefront of its ambitions. “This collaborative approach allows us to anticipate the evolving needs of the marine electronics market and design products that align with those needs.”
Inspiration comes from team visits to shows such as SIBS, METSTRADE and the Consumer Electronics Show in Las Vegas, which Scanstrut attends looking for latest trends in both technology and marine.
Bowles says a noteworthy example inspired by exhibitions is Wireless Power Onboard. “That allows you to send power to lighting and other low wattage electronics around the boat without physical connection,” he explains. “This eliminates metal on metal wiring and the risk of corrosion onboard. This concept has not only made it to market but has undergone a meticulous development process, driven by valuable feedback from OEMs. It’s set to enter production and is expected to be available by 2024.”
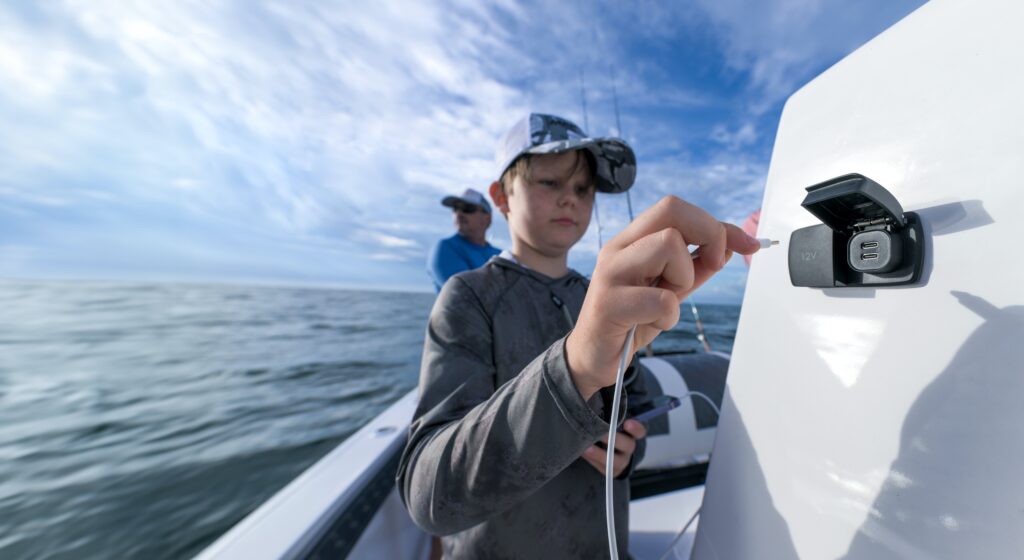
Like the above, Bowles’s aim for the next five years is to see the development of more complex custom electronics from Scanstrut.
“We are doing an increasing number of large projects,” he says. These are characterised by a combination of challenges and unknowns with significant team demand, extended development timelines, and complexity in design, manufacturing, and testing processes.
Enabling this, the culture which has grown up is of an open office, with all employees free to ask questions of each other. Brainstorming and workshopping are actively encouraged to push boundaries and the list of potential ideas is growing.
“In the next five years, I’d like to see more complex custom electronics of ours in the market. Displays, interfaces, wireless power etc,” finishes Bowles, and there’s not much that’s set to stop him.
The post In Focus: How Scanstrut’s in-house team beats drudgery appeared first on Marine Industry News.